It's likely that your company will at some point need to add onto an existing facility or establish operations in a new location. Whether this is because of business growth, a change in demographics or tax law, or another consideration, it can be a frustrating and time-consuming process. But with sufficient planning, your transition can be safely and smoothly completed, with minimum stress and maximum efficiency.
There will be important questions to answer: what are some challenges that you may face as you make this transition? What steps can you take to streamline the process? And how can you make sure that important safety and OSHA compliance considerations (including rooftop safety) are included in your plans? The following information can help.
Common Challenges
There are many challenges in the process of relocating production to a new facility. These can include legal, financial, and logistical issues. Some common pain points for companies could include:
- Downtime for production machines. Obviously, the more downtime your facility experiences, the more profit your company loses.
- Inaccurate/incomplete layouts. Oftentimes layouts of the donor facility do not completely or accurately represent the current locations for equipment, along with any necessary additions to the production line (e.g. overhead conveyor belts).
- Missing equipment or accessories during the transition. A move to another facility is a massive undertaking, and it is all too easy to misplace vital pieces of equipment in the transferal process.
- Unsafe work areas. Many times a new facility will not be up to the previous facility's safety standards. It is critical to make sure that OSHA safety guidelines are followed, even before a facility becomes fully operational.
With these and other challenges facing you, what can you do to ensure a smoother, safer transition?
Steps You Can Take
Detailed, advanced planning can prevent the waste of time and resources in the future, and result in a seamless move without unnecessary hazards to your employees. Here are some steps you can take:
Carefully check and confirm your equipment layouts. This should be one of the very first steps in the moving process. All layouts from your current facility should be checked for accuracy and completeness, so that no unexpected issues come up in the new facility. It is a good idea to confirm your layouts' accuracy by spot checking. You should check not only for equipment dimensions and locations, but for overhead equipment, pits, trenches, aisle sizes, and other operational considerations.
- Review the new facility for adherence to safety standards. Even if your designated facility is not yet at full operational capacity, if employees or contractors are on site, it is imperative that OSHA guidelines are conscientiously followed in and around your new facility. Roof fall protection systems are a critical component of workplace safety. For example, OSHA standard 1926.501(b)(1) under "Unprotected sides and edges" states that:
“Each employee on a walking/working surface (horizontal and vertical surface) with an unprotected side or edge which is 6 feet (1.8 m) or more above a lower level shall be protected from falling by the use of guardrail systems, safety net systems, or personal fall arrest systems.”
If your new facility is not yet up to par, take decisive action to correct matters.
- Perform an equipment review. Along with a careful review of the layouts, inspect your production equipment long before moving day comes. Pay special attention to where access panels and utility connection points are located.
- Tag or ID all pieces of equipment. The best way to avoid lost equipment during the move is to take a detailed inventory of every piece of equipment, down to the nuts and bolts if needed. Besides keeping a written inventory log, it is also a good idea to take detailed pictures of each part. Also, keep a record of which crates, trailers, and/or carriers are matched to specific pieces of equipment.
- Work out a moving schedule that limits downtime. As mentioned previously, you want to limit the downtime on production as much as possible. Therefore, it is vital that you craft a schedule for moving that allows your current facility to stay in operation until the new facility is ready to receive all of the production machinery. Some schedules allow for limited production, and a gradual phasing out of operations; others call for a quick move that only halts production for a few days. Circumstances vary, so you will have to determine what is best for your particular business model.
- Follow OSHA safety precautions. Be sure to follow appropriate OSHA safety precautions as you move in. For example, when inspecting roofing conditions of performing installation and maintenance on rooftop equipment during your move or new opening, you need to set up rooftop guardrails and other roof fall protection systems according to relevant OSHA guidelines.
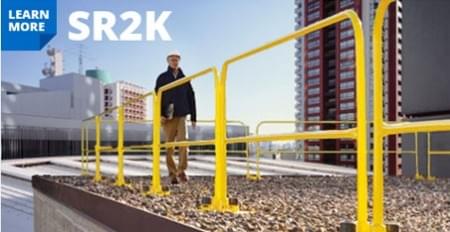
Implementing Roof Fall Protection Systems
Rooftop safety is a key component of a successful move. Even if you anticipate that roof work and access will be rare, it is extremely important that you have rooftop guardrails and other roof fall protection systems in place whenever an employee is required to access the roof. It is critical that rooftop fall hazards are identified and promptly addressed, in accordance with OSHA standards. That way any preventable accidents or fines can be avoided on day one of your new facility.